Are you curious about how the THY Precision Injection Molding Optical Lenses process step by step combines optical and mechanical design in making high-quality lenses? This blend is changing the game in optical manufacturing. It lets us make innovative products that meet the market’s changing needs. Let’s dive into this article to learn more about this advanced technique and how it can improve your optical lens production.
THY Precision is a top name in precision-molded optics. They’ve perfected the Injection Molding Optical Lenses process step by step. This lets them create optical lenses that are top-notch in performance and efficiency. By combining optical and mechanical features, they’ve made a solution that boosts product performance and makes production smoother, offering great quality and saving costs.
Key Takeaways
- Understand the basics of the Injection Molding Optical Lenses process step by step and its role in blending optical and mechanical design.
- Learn about the materials and properties used in making precision-molded optics.
- See the important steps in the Injection Molding Optical Lenses step by step cycle, from designing the mold to checking quality.
- Find out how THY Precision has become a pro at the Injection Molding Optical Lenses step by step to offer new optical solutions.
- Discover the wide range of uses for precision-molded optics and the future of the industry.
The Fundamentals of Injection Molding Optical Lenses
At THY Precision, we know the injection moulding process is key for making top-notch optical lenses. It’s a step-by-step process that blends optical and mechanical design. This ensures the lenses are precise and work well. Let’s explore the basics of this process.
Optical and Mechanical Design Integration
The first step is blending optical and mechanical design. We plan the lens shape, how it’s mounted, and its functions carefully. This planning is vital for the injection moulding to work well.
Mold Design and Fabrication
After designing, we focus on making the mold. It must be made just right to produce the lenses accurately. This is key for making high-quality, precise optics through the injection process.
Injection Molding Optical Lenses Process Step | Description |
---|---|
Plasticization | The polymer pellets are heated and melted in the injection unit, creating a homogeneous molten material. |
Injection | The molten plastic is forced into the mold cavity under high pressure, filling the mold and taking the desired shape. |
Cooling | The plastic in the mold is allowed to cool and solidify, taking on the final shape of the part. |
Ejection | The solidified part is ejected from the mold, completing the injection molding cycle. |
Understanding the injection moulding process helps THY Precision make precise optical lenses. We focus on design and mold making to meet high standards.
Materials and Properties for Precision Optics
Choosing the right polymer for making precision optical parts is key. Amorphous and semi-crystalline polymers are top picks because they work well for optics. They keep their shape and don’t change much when used in the injection molding procedure.
Amorphous Polymers: Optical Clarity and Stability
Cyclic olefin copolymers (COCs) and cyclic olefin polymers (COPs) are known for their clearness and staying power against the elements. They don’t soak up much water and handle heat well. This makes them perfect for tough optical jobs. The thermoplastic injection process makes these materials reliable for polymer injection molding phases and injection molding cycle steps.
Semi-Crystalline Polymers: Dimensional Precision
Semi-crystalline polymers are better at keeping their shape than amorphous ones. This is great for parts that need to be very precise. But, making these parts requires more careful control in the injection moulding process step by step to get the right look and quality.
Polymer Type | Optical Properties | Dimensional Stability | Processing Considerations |
---|---|---|---|
Amorphous Polymers (COCs, COPs) | Excellent optical clarity, low water absorption | Good | Consistent polymer injection molding phases and injection molding cycle |
Semi-Crystalline Polymers | Good optical properties | Improved dimensional stability | Require more careful injection moulding process step by step control |
Picking the right polymer is key for making precise optics with injection molding procedure. Knowing how amorphous and semi-crystalline polymers work helps makers get the look and quality they want.
“The choice of polymer material is the foundation for success in precision optical injection molding.”
Mastering the Injection Molding Optical Lenses Cycle
THY Precision leads in making precise optical parts. They know how key it is to master the Injection Molding Optical Lenses cycle. This process has many steps, each one vital for making top-notch optical lenses and parts.
TheInjection Molding Optical Lenses cycle starts with melting and controlling the flow of thermoplastic resinmouldingtechniques. First, the raw material gets heated and made into a uniform melt. This melt is then injected into the mold.
Then, the Injection Molding Optical Lenses take over. The molten material spreads out evenly in the mold, capturing tiny details. This step is watched closely to avoid mistakes in the final product.
As the part cools in the mold, the Injection Molding Optical Lenses moves on. It goes through steps like cooling, packing, and holding. These steps make sure the part has the right optical and mechanical properties.
Finally, the finished optical part comes out of the mold. This ends the Injection Molding Optical Lensescycle. THY Precision gets great at making optical lenses and parts by doing each step well.
Injection Molding Process Step | Key Considerations |
---|---|
MaterialMelting | Precise temperature control, uniform melt quality |
MoldFilling | Even distribution, minimizing defects |
PartSolidification | Cooling, packing, and holding parameters |
PartEjection | Gentle removal, maintaining part integrity |
By getting each part of the Injection Molding Optical Lenses cycle right, THY Precision makes high-quality optical parts. These parts meet the toughest industry standards.
“Precision and control are the hallmarks of a successful Injection Molding Optical Lenses” – THY Precision Engineering
Integrated Production and Quality Control
At THY Precision, we know making precision-molded optical lenses needs a mix of advanced steps and quality checks. Our top-notch injection molding makes sure we produce optical parts that are precise and meet high standards.
We use automated machines and systems to keep quality high. These machines work with special software to watch over the molding process. This way, our experts can fix any problems fast, making sure our products are top quality.
We also use special methods to check our work. These methods help us spot and fix any issues during the molding process. This makes sure our products are up to the highest standards.
Key Injection Molding Process Step by Step Capabilities | THY Precision’s Advantages |
---|---|
Automated Injection Molding Machines | Consistent production of optical components |
In-line Metrology Systems | Stringent dimensional and optical performance control |
Advanced Process Monitoring and Control Software | Real-time identification and resolution of deviations |
Comprehensive Quality Control Procedures | Delivery of high-quality, precision-molded optical lenses |
THY Precision combines the latest in injection molding to make top-notch optical products. Our focus on quality makes us leaders in the precision optics field.
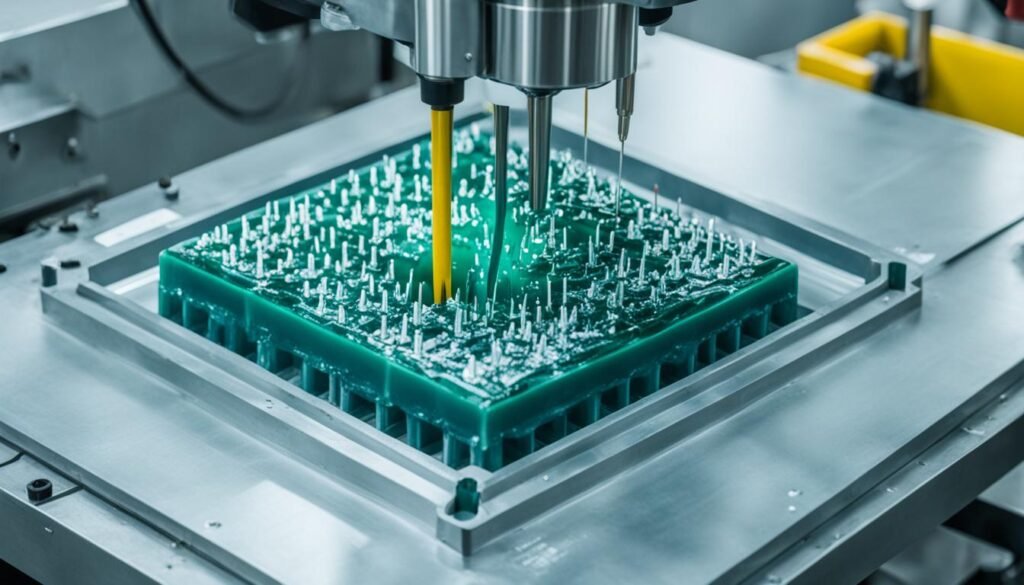
Applications of Precision-Molded Optics
The injection moulding process step by step has changed how we make precision-molded optical parts. These parts are now key in many industries. In cars, they help with rain sensors, displays on the dashboard, and sensors for steering angles. This makes driving safer and helps drivers more.
In the field of health, these plastic molding steps parts are used in devices for diagnosing, magnifying scales, and syringes. They make patient care better and more precise.
These resin molding techniques are not just for cars and health. They also help in making lights and lasers work better. For example, they’re used in detectors, lenses for lasers, and in systems that scan things.
Companies that make consumer electronics and handle goods also use these polymer injection molding phases parts. They’re in scanners, photosensors, and devices that store data. This makes things work better and faster.
The injection molding cycle is great because it’s affordable and can make lots of parts. As we need more advanced optical tech, using precision-molded optics will keep being important. This will help many industries move forward.
Industry | Applications of Precision-Molded Optics |
---|---|
Automotive | Rain sensors, head-up displays, steering angle sensors |
Life Sciences | Diagnostic devices, scale magnifiers, syringes |
Illumination and Laser Technology | Motion detectors, collimation optics, laser lenses |
Consumer Electronics | Scanner systems, photosensors, optical storage devices |
Logistics | Scanner systems, photosensors, optical storage devices |
THY Precision’s injection unit operations and molding machine functions have made high-quality, affordable optical solutions possible. By using the injection moulding process step by step, THY Precision keeps pushing the limits of what precision-molded optics can do. This helps many different areas of life.
“The versatility and scalability of the injection molding process make it a valuable tool for meeting the growing demand for high-performance, cost-effective optical solutions.”
Advancing Optical Design with Injectionmouldingprocessstepbystep
The injection moulding process step by step opens up new design possibilities. It lets optical engineers improve optical performance and functionality. This process combines optical and mechanical features. It makes complex lens shapes like diffractive and aspheric ones possible without extra cost.
This flexibility and automation make it great for making many high-precision optical parts. As the process evolves, combining injection moulding with optical design is key. It will help create next-generation optical systems for many uses.
The mold filling and injection unit operations let engineers try new solutions. This opens up new chances for better optical performance. Designers can now make complex lens shapes that were hard or impossible before.
“The injection moulding process step by step has revolutionized the way we approach optical design, empowering us to create optical components that push the boundaries of what was once thought possible.”
As the industry uses injection molding more, combining optical and mechanical features will grow. This lets manufacturers make complex, yet affordable, optical solutions. These solutions are for a wide range of applications, from consumer tech to medical devices.
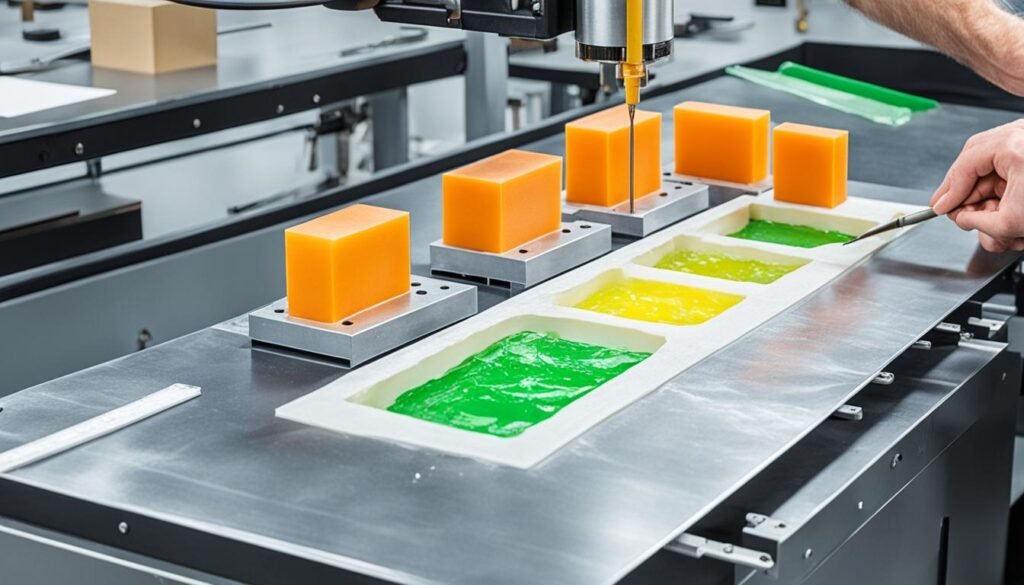
THY Precision leads in injection moulding solutions. They work with optical designers and use the latest in injection molding. This has helped their clients improve their optical systems, bringing new performance and innovation.
Conclusion
The blend of optical and mechanical features in injection moulding has changed the game in precision optics. THY Precision has become a leader by understanding the details of the process. They excel in plastic and resin molding, making them top in thermoplastic injection and polymer molding.
THY Precision uses the injection moulding process to mix complex optical and mechanical designs. This has opened up new ways to make high-quality, yet affordable, optical parts. They know every step from filling the mold to the final operations, ensuring top-notch optical performance and quality.
As the need for advanced optics grows, the advancements in injection moulding will be key to the future of optics. THY Precision is at the forefront, leading with their innovative technology. They are a reliable partner in the precision optics field, ready to shape its future.